Apatin Brewery’s modernization with with KHS

Founded in 1756, Apatin is the oldest brewery in the Balkans and the Molson Coors Group. The Serbian plant run past Molson's subsidiary Apatinska Pivara Apatin has relied on KHS technology for over four decades. The Jelen beer brand is especially well known. The partnership betwixt the two companies was recently farther cemented by conversions to two of the brewery'due south glass lines and the procurement of a KHS Innofill Can DVD can filler. Every bit a upshot of the all-encompassing modernization, Apatin Brewery has been able to greatly optimize its line efficiency and production quality. The traditional brewery also benefits from improved hygiene and savings in energy and media.
The cooperation betwixt Apatin Brewery and the Dortmund systems supplier dates back to the 1970s and to KHS' predecessor companies Holstein & Kappert and Seitz Enzinger Noll Maschinenbau, who in 1993 merged to form KHS. "Nosotros've always had a really reliable partner at our side in KHS. Its personnel know not only our production site and technology within out; they're also familiar with our requirements and all possible challenges," smiles Tanja Popović, packaging managing director at Apatin Brewery.
When in 2014 the brewery decided to modernize a few of its machines – some of them almost 20 years former – it again went for sustainable systems from its long-term partner KHS. The mechanical technology visitor beginning renewed two glass lines and in 2022 the customer and then invested in the Innofill Can DVD can filler. "Our old machines could no longer run across our current demands regarding production quality, performance and sustainability," Popović explains. "Together with our colleagues from KHS, nosotros devised a sophisticated concept for modernizing our lines."
Resource savings and improved economic system
KHS started revamping the offset drinking glass line back in 2014. The brief was to reduce media and electricity consumption on the bottle washer. By installing ECO carriers the KHS engineers considerably optimized the resource efficiency and economic system of the system. "The machine now not only uses a lot less water and caustic and fewer additives; it also consumes less energy," states Bojan Culibrk, KHS' local service managing director.
Just iv years after Apatin Brewery took the next stride towards sustainable product past modernizing one of its glass fillers. The KHS specialists replaced the erstwhile vacuum pump with a new ECO variant that feeds process water back into the system after treatment. "On the one manus, we've cut media consumption, and on the other, the filler is now more than economical and more efficient," says Culibrk. The ECO vacuum pump proved so convincing that the Serbian bottler also procured this slice of equipment for its 2d glass filler.
Optimized product quality and less wear
The traditional brewery, founded in 1756, also commissioned KHS to install a new capper turret. This is a lot easier to clean than the previous model, Culibrk explains. "It lowers the risk of product contagion and as a result, hygiene is improved." Furthermore, KHS was also able to optimize the cap quality on the drinking glass bottles.
In addition to improved hygiene and production quality, the Serbian beverage producer as well wanted to automate its institute technology. This has been accomplished past using HMI panels integrated on the glass lines and new can filler. Co-ordinate to Popović, this makes the automobile much easier for operators to use, as all sequences are automatic and many of them have been digitalized. "The new programs for production changeover, sanitizing and filling speed up our processes. Using this state-of-the-fine art engineering science, nosotros accomplish a much college level of production efficiency and avert unplanned downtime thanks to improved safe and reliability in filling," says Popović. The HMI system also detects wear parts in advance, meaning that replacements tin can be ordered in good time.
Sustainable and efficient drink canning
In 2020, the brewery then ultimately invested in an Innofill Tin can DVD filler. "We had to boost our capacity in this segment in order to meet the growing demand for beverages in cans," Popović declares. "With our new filler we can process up to 25,000 0.5-liter cans an hour. We're as well more efficient and sustainable."

Photo KHS
According to the company's ain statistics, the output runs to more ii million hectoliters per annum. On the Innofill Tin can DVD it fills all of its brands into containers holding 0.33 and 0.5 liters, amid them Jelen, Jelen Chill, Jelen Cool, Apatinsko, Staropramen, Bavaria, Nikšićko and Nikšićko Tamno. The brewery importantly supplies the regional market place, namely Serbia, Montenegro, Republic of bosnia and herzegovina, Croatia, Northern Macedonia and Slovenia. Popović is non ruling out expansion, still. "With its high chapters and efficiency, the new filler provides ideal conditions for this."
Optimum hygienic filling weather
Besides the high throughput, hygiene and product quality too played a key role when making the new investment. The Innofill Can DVD permits warm filling of beverages at around 20°C. This method becomes more than significant specially regarding the further processing stages as information technology practically eliminates the germination of condensation. This more than or less rules out the chance of cartons, trays and cans in six packs growing soggy, forming mold or being contaminated by microbes.
The brewery is also convinced by the new COtwo purging process that has an equally positive impact on the product quality, every bit Culibrk comments. "Oxygen pickup impairs the quality of the potable. In order to prevent this, in modern production containers are purged with COtwo." The KHS purging process is so efficient that less oxygen enters the containers compared to using conventional methods – despite lower amounts of carbon dioxide beingness used. Moreover, the volumetric filling principle also improves the filling accuracy.
Installation despite the Covid-19 pandemic restrictions
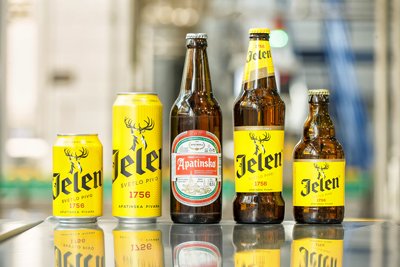
Photo KHS
The tin can filler was installed during the Covid-19 pandemic and nether the restrictions imposed by this. "Thank you to our local presence in Serbia and the Balkans, we were able to carry out all work apace and efficiently. Travel restrictions and social distancing of course presented us with a challenge or two during the class of our day-to-day activities. However, together with the customer nosotros managed to bring the project to a successful close within the given schedule," Culibrk smiles. Popović as well draws a positive decision. "The dedication and delivery shown by the KHS team have left a lasting impression on the states. We were always able to rely on them and their expertise." This is why KHS will continue to be commencement choice for Apatin Brewery when it comes to expanding product or procuring new technologies.
giddingsdigetund66.blogspot.com
Source: https://packagingsouthasia.com/events/apatin-brewerys-modernization/
Belum ada Komentar untuk "Apatin Brewery’s modernization with with KHS"
Posting Komentar